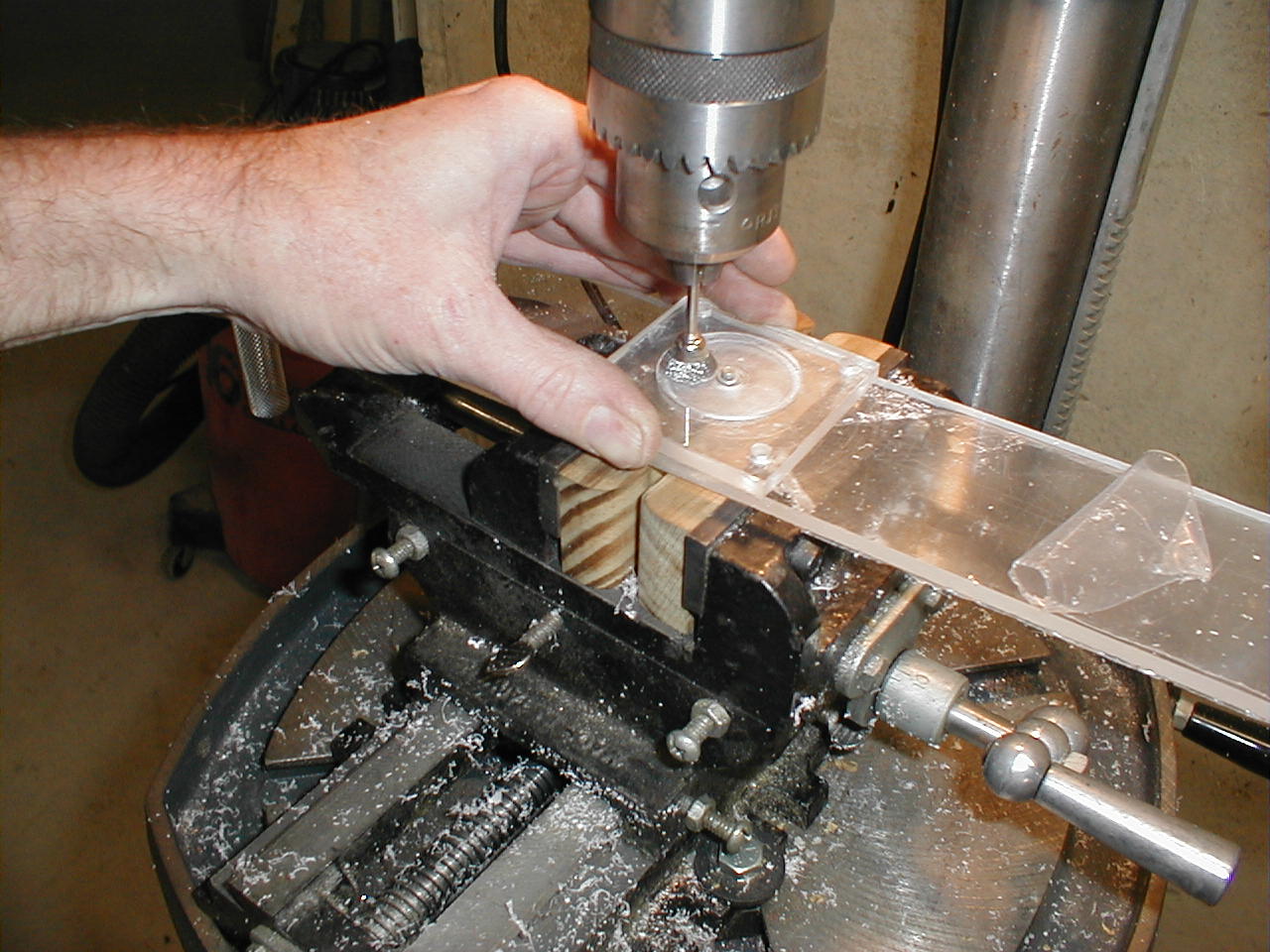 |
After
laying out the parts in AutoCad, cutting the patterns, and transferring
the patterns to the acrylic, I began cutting and milling the
parts. The first of the tricky cuts was the stepper motor
mount. "Tricky" is relative, but trying to mill on a drill press
is tricky!
To get the recessed circle routed out of the acrylic, I used a shaft
that was the same size as the hole in the center of the mount and
rotated the part around the shaft. The second piece of acrylic
below the motor mount was rotated along with the mount to prevent
scratches on the bottom of the motor mount. This piece turned out
almost perfect with the raised step on the stepper motor fitting snugly
into the recess on the mount.
|
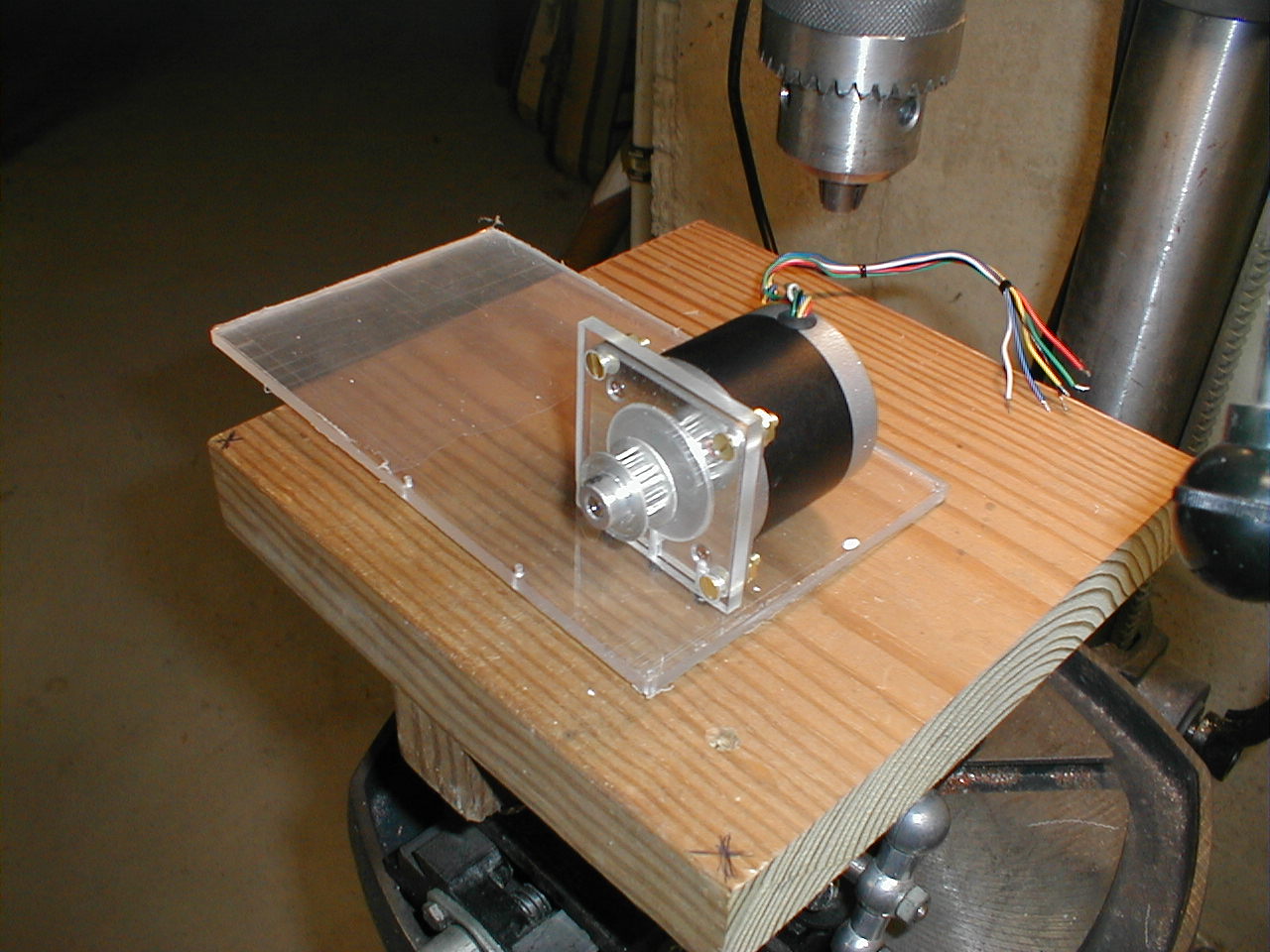 |
Here,
the motor is attached to the mount and the mount is attached to the
base of the tilting camera mount. While it looks like the base of
the camera housing is way too wide, the piece will be cut after the
left-most of the three holes in the front of the base.
I assembled each new piece as soon as it was finished not only to make
sure that the parts fit, but also to admire my work. ;-)
This was a fun project to build and I was in no rush to finish it.
|
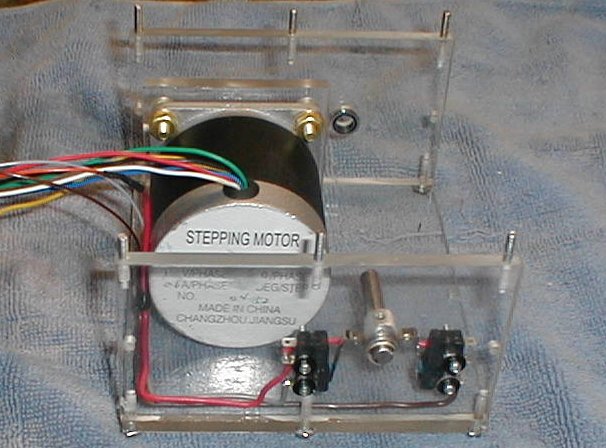 |
Four
pieces done. The1/4" by 3/8"
flanged
bearings are visible in both end pieces.
In the foreground of the picture, you can see a stub of an axle with a
hand ground cam lobe that actuates the roller equipped
micro-switches. These switches are adjustable with a total of
about 1/4" of travel. They are used to limit the amount of total
tilt that the camera will be allowed to move.
The cam lobe is also adjustable by means of a set screw in the center
of the lobe. The hole is smaller in diameter than the roller on
the micro-switch, so the roller glides right over the hole. I
must have spent a half hour envisioning how the unit would tilt before
I was sure that the switches were wired correctly.
|
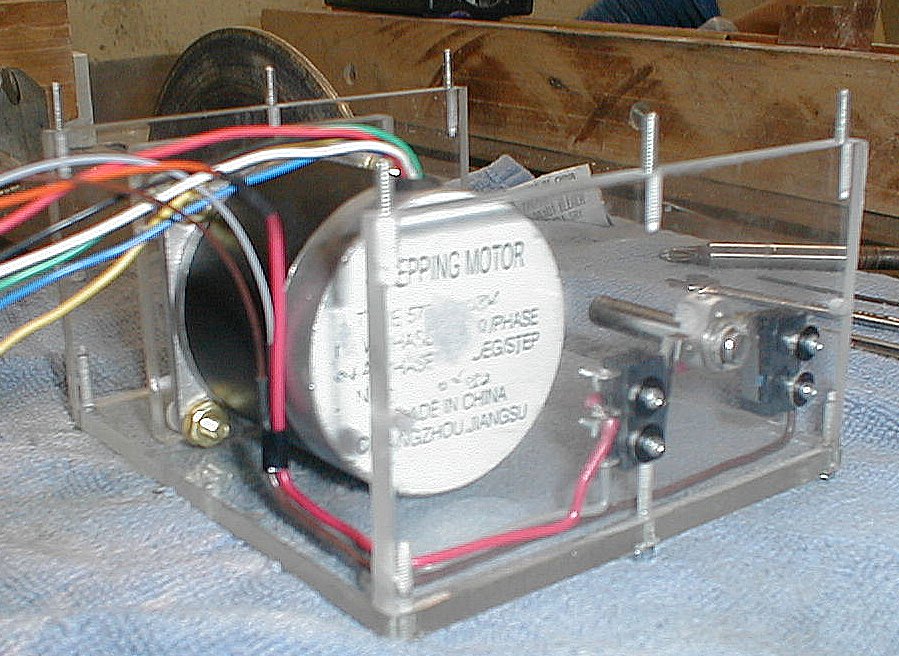 |
Another
shot of the cam lobe and micro-switches. The height of the cam
lobe is easier to see in this shot.
The black washers are rubber coated to seal the oval adjustment holes
for the switches. The bearings also have plastic seals and I
packed the bearings with silicone grease to make sure that water could
not enter the housing.
Even though the camera will be placed under the eaves of the house, we
get violent storms in the summer and horizontal rain is not that
uncommon. Hopefully I will get a year or so of service from the
tilt and pan mount before it will need to have the bearings repacked
with silicone grease.
|
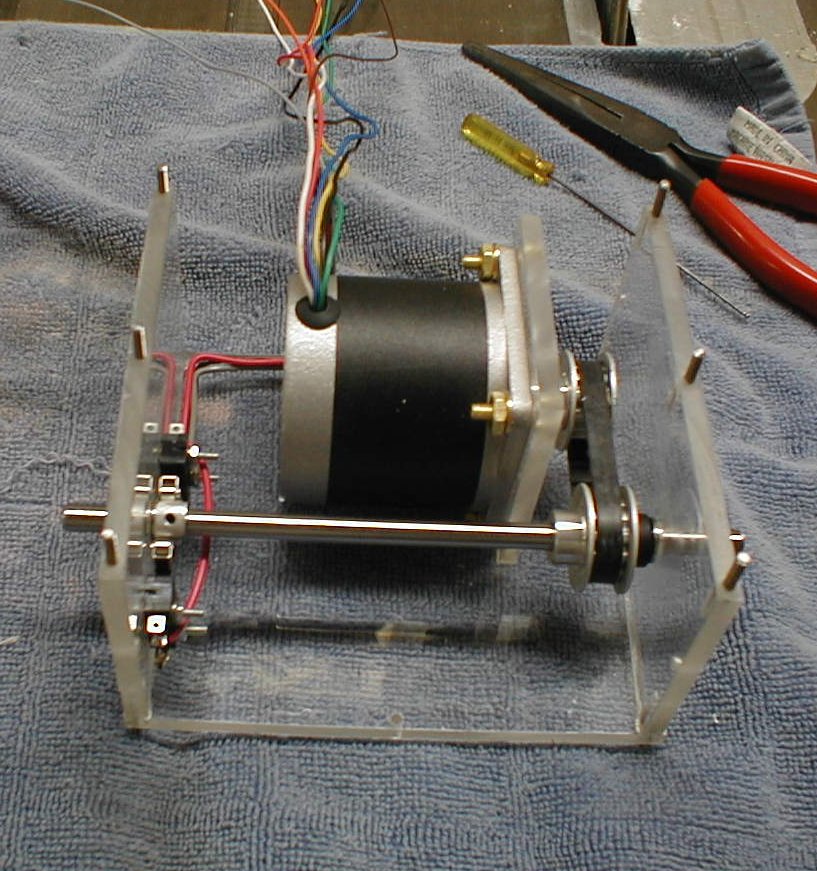 |
The
first critical test of my measuring, cutting and drilling came when I
installed the pulleys and toothed belt. I ended up with
deflection of between an eighth to a quarter of an inch. Perfect.
It pays to, as the saying goes, measure twice and cut once.
If there had been a problem with the belt being too tight or too loose,
I would have just needed to recut the bottom plate. Not too time
consuming, but nice that it fit right the first time.
At this point in the assembly, with the motor offset quite a way from
the axel shaft, it seems hardly possible that I have calculated the
weights properly so that the camera and housing will balance perfectly
on the axel, but I will have to trust that my calculations are correct
as I won't be able to check it until the camera is mounted.
At least I know that the distance between the motor and shaft was
right, so the chances that the rest of the equation will work is on
track.
|
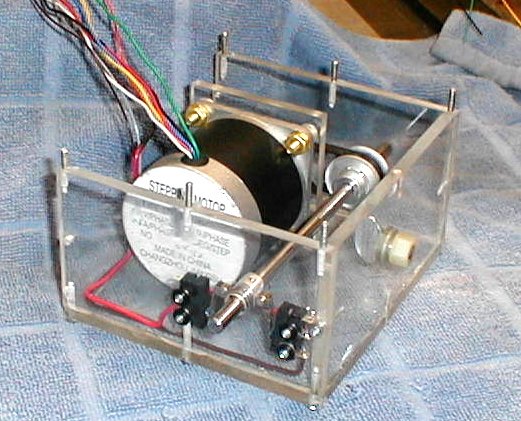 |
The
front plate of the tilt housing is mounted. The camera is mounted
a bit below the center of the plate, on the same plane as the motor and
axel shafts.
While the stepper motor sits flush with the floor of the housing, there
is about 3/8" of space above it, between the top of the motor and the
bottom of the top housing plate. This is to allow for the wires
coming out of the stepper motor.
I haven't mentioned it, but the lateral play in the axel shaft is
adjusted with axel shims from an Associated RC-10 radio controled
car. Both the pulley and cam lobe for the limit switches have set
screws to hold them securely and the shims go between the pulley / lobe
and bearing. The bearings are flanged with the flange to the
inside.
|
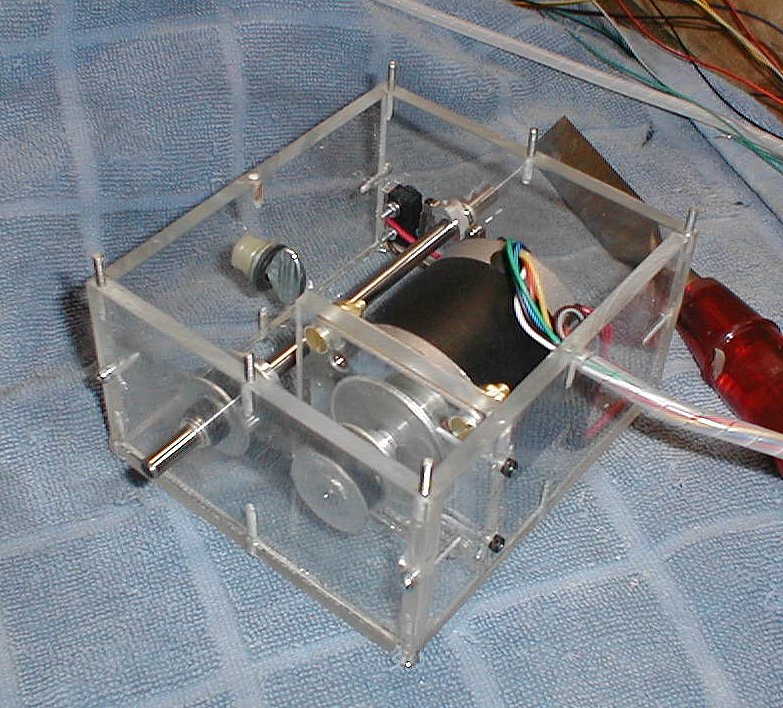 |
The
rear plate gets attached. The hole at the top for the 6 motor
wires, 3 limit wires, and eventually another 3 microphone wires in a
shielded cable and the composite camera power and video feed wires will
all come from the rear of the camera housing and terminate in the box
that will hold the pan assembly.
The chisel with the red plastic handle is about 40 years old. It
was one of my dad's tools and now a cherished one of mine. It still
holds a great edge after decades of being honed on an oil stone and
deburred on a leather strap. It is also a great tool for shaving
small bits of plastic to make sure that the plates filt together
perfectly.
Once the entire tilt housing has been assembled and checked for fit, it
will be sealed with a special acrylic adhesive that is as thin as water
and applied with a syringe with a fine needle. The adhesive will
|
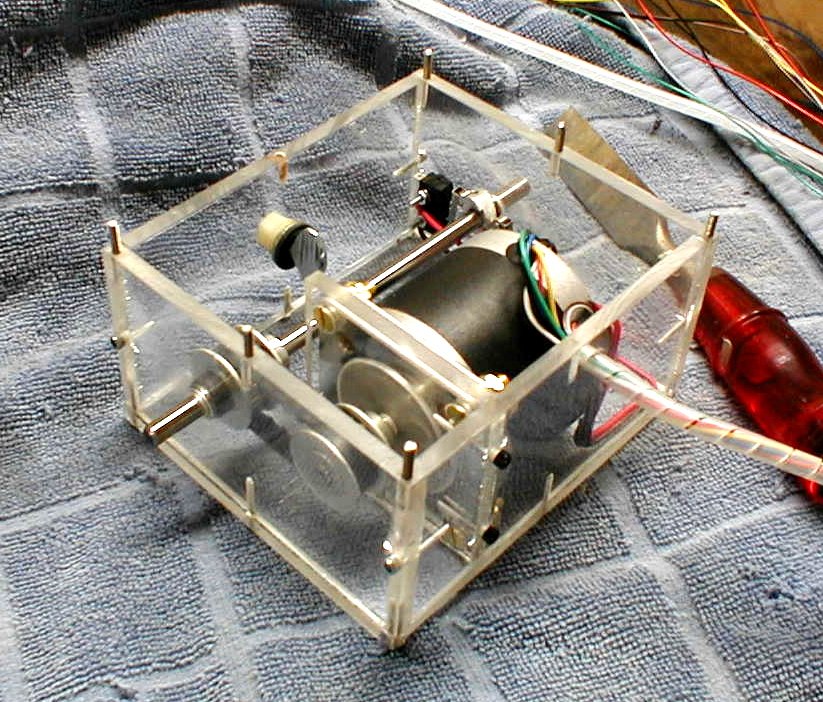 |
be
"wicked" up between the joints similar to a "sweat joint" when
soldering plumbing. I didn't have a lot of experience with this,
so I used many of the scraps of acrylic that I accumulated to
practice. This adhesive is really thin! It also leaves
visible traces of itself any place it comes in contact with. The
adhesive works by softening up the acrylic and needs perfectly mated
joints and some pressure to work.
I'm glad that I took the time to do some research on "gluing acrylic"
before I tried it, as I am sure that I would have ruined the parts if I
hadn't practiced first.
You can find a lot of information on working with acrylics by searching
for acrylic diy build aquarium.
|
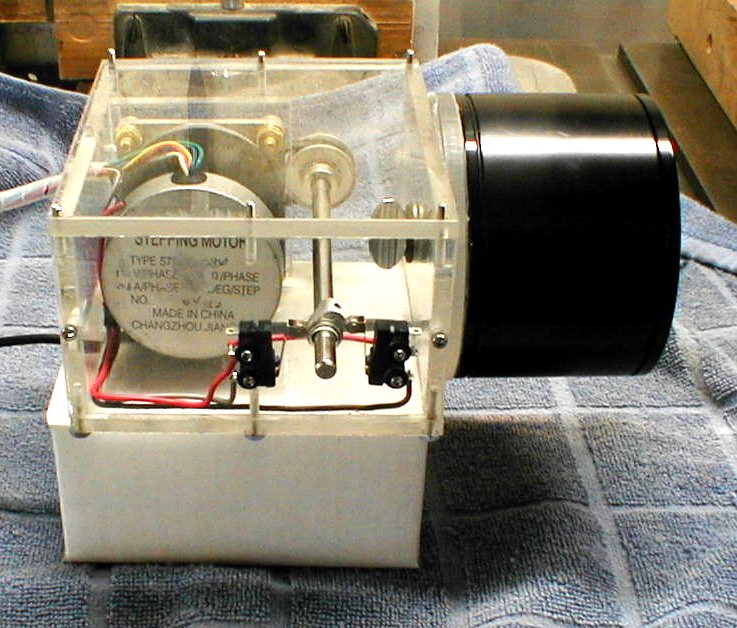 |
Finally
I get to put the top plate and the camera on to check for
fit. It fits pretty well.
The round plate behind the camera is there to give me some additional
weight in the front to help balance the tilt housing and camera.
I have figured the balance point almost perfectly. With the plate
in place, it is a little heavy on the camera end. If I remove the
plate, it changes to be a little heavy toward the rear. Once I
mount the microphone plate, I won't need the acrylic disk and the
balance should be close enough that the force of the permanent magnets
in the stepper motor will hold the camera and tilt housing at whatever
angle I need.
The thumb screw that holds the camera in place will allow me to make
sure that the camera is positioned properly and then cinch it down.
|
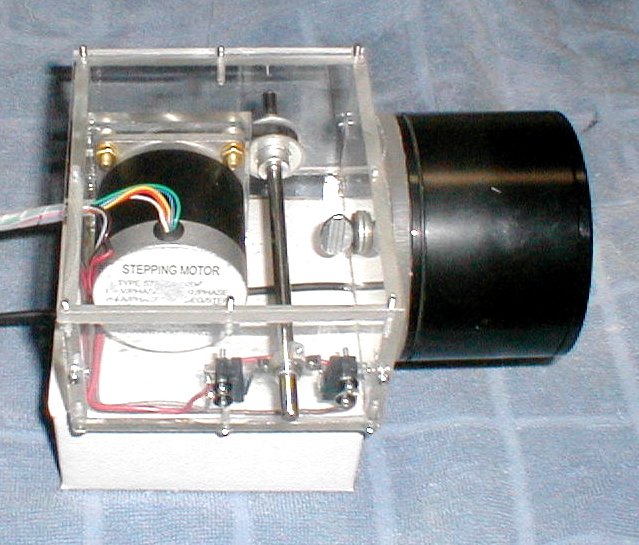 |
Tonight
I hooked the camera up to the A06 controller and ran through a few
commands to make sure that the limit switches were doing their job
properly. I had to adjust them both a little to get them to allow
the desired 135° of movement.
The camera will be mounted under the eaves of the second story of our
home, above the front door. I would like for the camera to be
able to look straight down so that I can see who is at the door.
The upward angle should be enough to see over the tree in the front
yard and on to the horizon beyond and the line of trees that is at the
end of its line of sight. That should be handy for seeing weather
related information such as the trees swaying or rain and snow hitting
the leaves or branches.
In the summer, I will be able to view the driveway and sidewalk, but a
lot of the front yard will be obscured by the large flowering plum
tree. In the
|
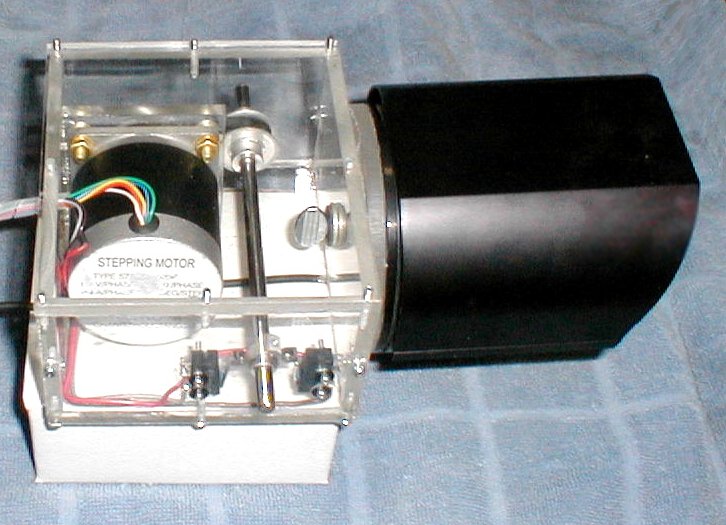 |
winter,
I should be able to view almost the entire front yard due to the leaves
being gone from the tree.
The sun shade is test fit on the camera. It is made from a light
weight plastic extrusion and doesn't add much weight to the setup.
This evening I spent about an hour and glued up the tilt housing.
It went pretty well with just a couple of places where the acrylic
adhesive got on places where I didn't want it. I buffed these out
the best I could and unless you are really looking for them, you
wouldn't see them.
Time to move on to the pan assembly.
|