
Back to the garage to do another repair on my truck. The engine oil pan rusted through. After a temporary repair with epoxy, it was time to fix it right. The job turned out to be not as much of a hassle as I had thought it would be.
I have another scraping project coming up and I thought it was time to make a proper copy of the King Way alignment tool. I think that this tool will help me to keep the ways parallel and plumb on the new project.
The last of the shaper projects has been finished. I've made a new crank handle. Now it's time to ask the shaper to earn its keep.
Time to stop the shaper from trying to walk across the floor. I learn how to attach a machine tool to concrete. This project
made a big difference in the way the shaper operates. Well worth the time and effort.
With the shaper now able to make more accurate parts, I wanted to turn a new ball handle to replace the single nut where the ball handle should have been.
Since I didn't have a ball turner, I had to make one. The project turned out looking good and all I need to do before I put the shaper to work is to attach it to the concrete floor.
I have finished tuning up the vise. The test cuts came out pretty nice. The table and vise are square with the ram, but there were another couple of issues to deal with. One of these days I just might finish this project.
The shaper is getting closer to being done. I have finished scraping the table support and the boss that it rides on. I finally get to take a test cut to check the work on the tool head.
Still more progress on the Sheldon shaper. I have now scraped in the tool head and swivel block and put a new surface on the tool head lock. Hopefully I am getting closer to being able to plane the vise rails.
I have made some more progress on the Sheldon shaper. I have scraped the swivel base for the shaper vise and have scraped the vise body. The one remaining task to do to finish the vise is to cut the top vise rails. I am going to try to do this on the shaper, so I needed to adjust it to be as accurate as I can get it.
I have made some progress on cleaning up my Sheldon shaper. It is in pretty good shape, but it does have a few issues that need to be sorted out. I now have power to it and have made a couple test cuts. This has led me to pulling out my metal scraping gear to take care of a less than accurate vise. I haven't done any scraping in a long time, so I am enjoying the process.
While in the middle of the air conditioning repairs on my truck, an opportunity presented itself. This was a Sheldon 12" shaper being offered for sale by one of the members of a metal working group in the Washington D.C. area. I happened to be the first to say I wanted it. While I was trying to get cold air back into my truck, I spent time working out how I could get the shaper moved from its current location to my shop. The move went smoothly and I now have a shaper. I am looking forward to getting it hooked up and learning about its capabilities.
Shortly after we finally got the Jeep AC compressor replaced, the AC in my Dodge truck died. What should have been an easy air conditioner compressor clutch coil replacement turned into learning that the fuse box on the truck is much more than a fuse box. If you have never heard of Chrysler's Totally Integrated Power Module (TIPM) and own a Chrysler/Dodge/Jeep product, you may want to give this article a read.
One more vehicle repair. This one was interesting. A 2012 Jeep Wrangler JK where the AC compressor clutch had melted. After trying without luck to find a replacement compressor clutch, I decided to try and reclaim the one that had melted. Now we have air conditioning just in time for the snowy season.
I seem to be on a roll
with regard to vehicle repairs. My son's Dodge Ram developed a
case of the dreaded "death wobbles" a few weeks back. We
approached the problem by testing and measuring the front end
components and were able to get rid of the wobble. The story is here.
Another project from the
garage. While fixing an issue that caused my check engine light to
come on, I decided to take a look at the power sliding rear window
in my Dodge truck. This window has been inoperative for a few
years. What I found wasn't pretty, but I got it to work again. If
you're into DIY repairs, you might find it interesting. You can
take a look at the repair here.
While trying to get the
yard mowed for a family get-together, the mower deck on my little
Deere 317 garden tractor had some issues. It turned out that metal
fatigue caused the blade spindles to separate from the deck. A new
deck is around $1400, so I attempt to fabricate and weld in some patch panels. The mower lives, so I
guess I was successful.
I purchased a 1972 Deere
301 utility tractor/loader to help out with some landscaping
chores at the new home. When I got it, the front frame was about
ready to break loose from the tractor. I ended up splitting the tractor to repair it.
Having a loader should make moving dirt around a little more fun.
The last installment of the tiller
rebuild is up. After many hours of work, I finally get a chance to
till some soil.
I've got the third page up
on rebuilding the John Deere #33 tiller.
All that's left to do is take some measurements, then design and
fabricate a PTO to power it.
I've got the second page
up on rebuilding the John Deere #33
tiller.
I've been working on the new home,
so not a lot of shop time lately. However, we've decided that we
want a bigger garden next year. This means that I get a new toy. I
bought a Deere 33 tiller and am in the process of rebuilding it.
The story is here.
Note: (October, 2015) Notcatbar.com is no more. While I paid my hosting company for
both the domain renewal and hosting, monkeywrench hosting took the money
and let the domain lapse. Since the owner of monkeywrench hosting installed himself as the notcatbar domain's owner,
I have no recourse unless I want to sue. That's not worth my time. One of these
days, I may incorporate the story of this big old home we are refurbishing into
benchtest.com, but it will be a fair amount of work that I am not yet ready to do.
~ Jim
Happy New Year.
After months of planning and a lot of work, the last piece
of equipment has been moved into the new workshop. More pictures
of moving have been posted.
After the short sale from
hell we finally bought our new home in late September. Since
then we've been doing some work fixing up the place and I've been
trying to move the past two decades worth of tools I've
accumulated. Some pictures of the moving
have been posted.
Closing on the new home
should be next week. 4+ months after we made the offer. Short
sales are lots of fun. In the mean time, I put together a new bench for the South Bend 405 and
scrape in a model B saddle.
Still waiting on whether
the bank has accepted our offer. In the mean time I've put
together a sleeve hitch, hitch lift rod and a one bottom plow for
the garden tractor. Story is here.
Summer is here. After 7
months of looking, we've put in an offer on a home and are
enduring the slow process of trying to buy a short sale. We have a
contract with the seller, but not yet with the seller's
bank. If you want a quick transaction, avoid short sale
homes. However, if it turns out that we get the place, the hassle
will have been worth it and we'll finally have a bit of wooded
acreage, a spacious home and a nice sized detached shop.
Between house hunting and researching the short sale process, I've
managed to spend a little time in the shop and garage. Here's a
link to the latest quick project. I put
some Hummer H2 rims and tires on my Dodge Ram 2500.
I've spent the first
part of the winter doing some work on my new to me John Deere
317 lawn and garden tractor. It now sports power steering
adapted from a Deere 318 and 345. Here's the story.
To fix some ongoing
issues with my former hosting company, I've had to move to a new
one. If you're seeing this note, the new hosting provider has me
up and running. Happy New Year!
In the second
installment, I finish scraping the mill. It turned out to be a
lot more work than I had envisioned, but the good news is that
it's done and the mill is a great deal more accurate. The second
part of the adventure may be read here.
After talking about
trying to improve the accuracy of my Grizzly G3103 mill for 4
plus years, I have finally begun the project. In addition
to the issues I'd thought I'd see, I've come across some that I
didn't expect. The first installment is here.
More fun than a barrel of monkeys.
The workshop has been
invaded by kittens! If you're in the Northern Virginia or
Washington DC metro area and you're looking for a kitten, we
have a litter that arrived as a surprise. We really need to find
homes for these little fur balls. Please
take a look, or better yet, take a kitten.
I finally got around to
doing some repairs on the
Shumatech DRO-350. I also add a pair of glass scales to
the mill.
The final installment of
the Surface grinder rebuild. I finish up by overhauling the spindle.
I finish scraping,
Magnetic chuck repairs, coolant system and spindle
troubles The latest updates may be found here and here.
More scraping, more
lapping, and getting ready to build a copy of a lathe alignment
tool. The latest update may be found here.
Still scraping, but I
also do a little lapping on my granite straight edge. Also,
using the Automatic Generation of Gauges to prove flatness. This
installment may be found here.
I've spent most of my
free time in the last month working in the garage with a scraper
in my hand.I've made some progress on the surface grinder, but I
also made a mistake. You can read about it here.
After spending the last
year reading about machine repair and scraping and doing LOTS of
scraping, I have finally gotten to the point that I am going to
attempt a large scraping project. The project is a 1967 DoAll
D624-8 surface grinder.The first installment may be found here.
It has been a while
since I updated anything here, but there seems to be a lot of
email asking questions on how I like the Grizzly Mill after a
year of having it. So I came out of hiding long enough to do a
small piece on the mill. You can find it here.
Before I take a bit of a
break from the workshop to do some spring clean-up on our home,
I buy an old South Bend lathe and give it some TLC. A new tool is always fun.
I finish up the
Shumatech DRO with the addition of a Jenix scale and adding some
ball bearings to one of the calipers. You can take a look here.
I've been busy in the
workshop adding a digital readout to the mill. I've
finished the first stage of the project and am quite pleased
with the results. ShumaTech Dro-350
Digital Readout
I found another little
annoyance with the mill. This one got a temporary fix that
is working out well, for the time being. Spindle Noises
There's a new piece on moving the mill into the workshop.
There's an update in the
Workshop section.
My wife Susie has been volunteering at a local
organization that finds homes for homeless animals. I had the
opportunity to tag along last weekend. I must say that I was
impressed with FOHA. They
are located near the border of Prince William county, in Loudon
county, and serve the Northern Virginia and metropolitan
Washington DC area. They have been helping animals find good
homes for decades and currently have about180 dogs and cats in
residence. The kennels, complete with runs, for the dogs and
cottages for the cats are all air conditioned! The cottage
for the FIV positive cats even has a comfy couch so yours truly
could kick back and spend some time getting to know all the
residents.
Susie had told me that she had fallen in love with a bunch of
the cats and wanted to adopt at least one of them. We currently
have one cat and he's not used to sharing his home, so we
decided that we would become a"foster family" for one of the
cats and see how our cat Petey handled some company. We chose
a cat named Nubby who has a little problem with one of his hind
legs as we thought that he wouldn't stand as good of a chance in
finding a home as the others. He's a great little guy with a
super personality. Petey is feeling a bit threatened by his new
roommate, but he's getting a little more comfortable as the days
go by.
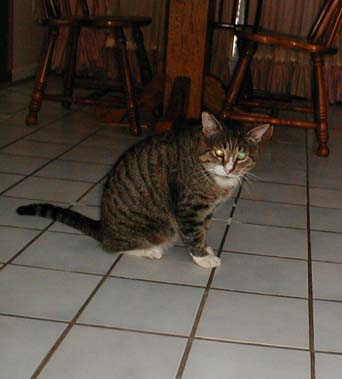
Click to Enlarge
So
why
am I telling you this? The answer is that FOHA has been
helping with the rescue and boarding of some of the animals
displaced by the flooding in the aftermath of Hurricane
Katrina and they have more animals than usual to find homes
for. FOHA really needs good homes for their dogs and cats.
If
an animal is unlucky enough to be homeless,but lucky enough to
wind up at FOHA, they are very well taken care of. All
of the dogs and cats receive a visit with a veterinarian to
get their shots and get checked over for health issues. The
volunteers make sure that all the cats get plenty of petting
and brushing and the dogs get walked through the beautiful
wooded countryside around FOHA (they have many acres) and get
washed, groomed and played with as much as possible.
If
you reside in the Washington DC metro area and have been
thinking about getting a dog, cat, or kitten, I recommend FOHA
highly. Please visit their website at http://www.foha.org/ or give
them a call for general information at 703-385-0224 or shoot
them an email at info@foha.org Their
website
even has pictures and a "BIO" on each of the animals.
Thanks
if
you can help out.
~
Jim
Geez it's been a long time since I have
posted. A lot of stuff has been going on and I am still
doing projects.It is just that the subject of the projects has
changed. The latest projects involve a security camera for the
house. I have been wanting to do this for a long time and
finally got started on it a year ago August. There was a lot to
learn, especially with the electronics side of it. I spent a few
months playing with preamplifier circuits and trying to become
somewhat proficient with circuit design software. I ended up
with a pretty nice little preamp for my old sound card to up the
clarity a bit. Some time in the future I will be incorporating
the preamp/sound card setup to help control my latest project, a
tilt-pan camera mount for my infrared assisted security camera.
You can take a look at the first tilt-pan mount and the preamp here.
At
this point, I am about to start on the third prototype of the
tilt/pan device. This one should be a fun project as I have
finally broken down and purchased a milling machine. I have
been wanting a mill for ages, so this is really a neat thing.
I
have cleaned up the site a bit and hope to start documenting a
few of the projects I have planned for the coming months. On
top of building another tilt and pan mount, I will be doing
some modifications to the new mill. I also want to build a
computer controlled circuit board cutting and drilling device
using the leftover stepper motors from the first tilt and pan
mount. The second tilt-pan mount was moved with servos, as
will be the third, so I have these extra stepper motors and a
controller... well, you know how that works... I can't just
let them sit and collect dust.
Well,
the
mill is supposed to arrive tomorrow and I'll try to document
the delivery and the subsequent move of this beast into the
basement workshop. That ought to be worth a laugh or two. This
thing is heavy!
That's
all
for now. Stay tuned for more to come.
© Fager 1998 - 2016