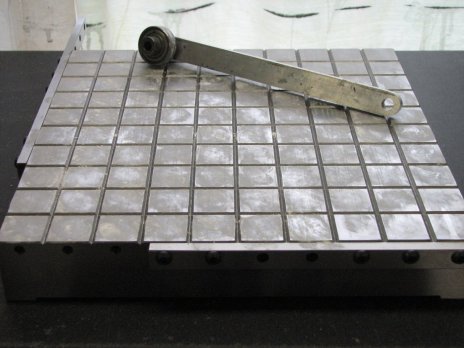
|
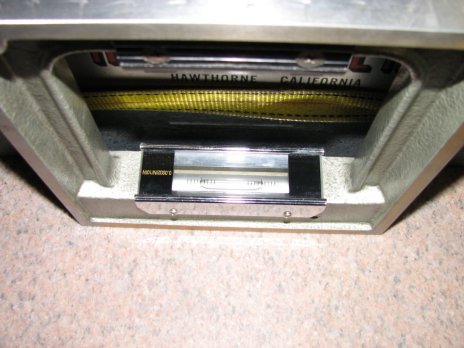
|
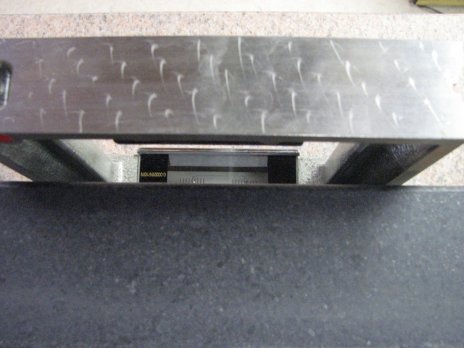 |
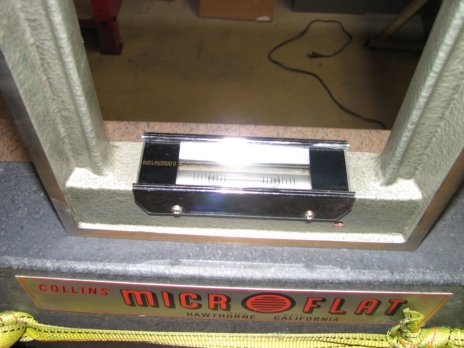
|
With a ball bearing roller to
apply the 3000 mesh diamond powder, I rolled it in as evenly as I
could. I then did a practice run on my carefully mapped old
surface plate. I then reapplied more diamond powder and carefully
lapped the top of the granite straight edge. After checking level
in front and behind the straight edge, I checked the top surface of the
straight edge. After a couple cycles, it was level and smooth.
|
After a few passes on the top surface of the straight edge, I set up my
measuring gear so I could check the relative height of the top
surface. This turned out to be as close to zero difference in
height as I can measure. For the last check, I leveled my new
Starrett surface plate with the straight edge centered on it.
When I had the bubble centered on my 0.0002" per 10" box level while on
both sides of the straight edge, I placed the level on the top
surface of the straight edge. In this position, the level also
centered the bubble. This was no surprise since the Supramess
indicator that I used to measure the relative height of the top surface
has much better resolution (20 millionths) than the level, but I was
happy for the confirmation none-the-less.
So, one more mini-project is done and I now have a way to check level
between the separated ways of the surface grinder. This should
help me to make sure that both the saddle and table on the surface
grinder stay level and square with the vertical column. As a part
of the project, I have now acquired a lap that I will use only for 3000
mesh diamonds. The 3000 mesh diamonds leave a pretty nice finish
on granite, but it would be nice to have one more lap that I can devote
to 5000 mesh only for situations where I would prefer an even finer
finish.