
Sheldon 12"
Shaper - pg. 5
September 28 to October 14, 2015
After finishing
scraping the tool head and swivel block and reworking the lock, I
decided that I had to paint the tool head. I really hadn't planned
on stripping and painting anything on this machine at present,
aside from shooting primer on the missing front panel and the
repair I made on a side cover. However, after all of the work I
had done on the tool head, looking at the two different colors of
flaking gray paint and all of the chips on the tool head made me
decide to spruce it up a bit. Since I have started down this
slippery slope, I will also paint the other parts I have repaired
and put primer on. At this point, I don't plan to paint the whole
machine. I would rather get some time in using it. I've had it
since the end of May and only have about two hours total time of
using it.
I used some aviation stripper, then wire brushed, then sanded the
tool head, taped it off, and shot a couple coats of primer on it.
I really can't tell if the darker paint below the light gray with
a bluish tint was another coat of paint or maybe a darker primer.
I like the darker bluish gray better than the lighter color, but
many of the Sheldon's I've seen pictures of match the lighter
color. While I had considered having the original paint matched
and going with some Benjamin Moore Urethane Alkyd Industrial
Enamel as I had done with my South Bend lathe, I decided against
it and purchased some Steel Gray paint from Tractor Supply. I also
purchased some black and some blue. I would attempt to come close
to the darker color by mixing the paint myself. I've used this
paint before on one of my tractors and it holds up pretty well. It
doesn't seem to chip as easily as some of the other enamels I have
used.
After I sanded the tool head with 220 grit paper and put the
second coat of high fill primer on the tool head, I had some time
to kill before calling it a night. My next scraping job would be
to scrape the boss that the table support rides on. I also needed
to scrape the bottom of the support itself. I hadn't decided which
surface to start with at this point. To get started with this job,
I first needed to map the surfaces I would be scraping. I set up a
magnetic indicator base on the bottom of the table and ran the arm
down toward the boss. I attached the DTI and measured the boss for
being parallel with the travel of the table and cross rail ways. I
measured in three positions: The rear side of the boss, the front
side and the center. All three measurements were within a couple
tenths of agreeing with each other across the length of the boss,
but the boss seemed to be out of square in two directions. The
boss was high on the left side by 0.0025". This was over 12 inches
of the 16.5" boss. Not terrible, but not to the Sheldon spec of
0.001" in 12" and I wanted to get it closer to 0.0001" if I could.
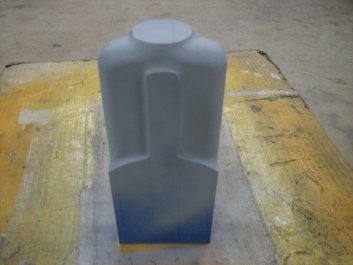
|
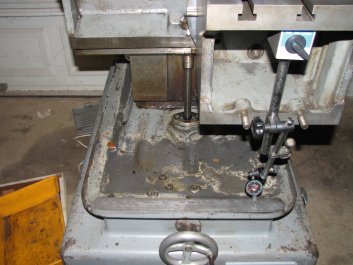
|
With
the old paint stripped off of the tool head, I gave it a
couple coats of high fill primer. Once it dried for 24
hours, I again sanded with 220 paper.
|
I
measured the top of the table support boss from left to
right. The boss was low on the right by about 0.0025" over
12". The boss is 16.5" wide.
|
The next step
was to measure the front to rear surface of the 1 9/16" wide (Y
axis) boss in relation to the top surface of the table. I had
previously measured the table in relation to the stroke of the ram
and after adjusting the ram gib, had proven that the ram and table
were in the same plane within 0.0001" over the length of the 12"
table. Now I wanted to get the boss to match the ram and table as
close as I could. I set my camelback straight edge on the table
and attached the mag base for the DTI on the under side or the
straight edge. I could now slide the straight edge across the
table and read the relative height of the boss. This boss was
angled a bit more than I figured it would be. About 0.002" in 1
9/16". That's a lot.
I decided to
check the table support to see if the bottom surface was 90° to
the mounting surfaces. I was surprised that I couldn't detect any
light between the vertical leg of the square and the two surfaces
that bolt to the front of the table. The support base is square
with the mounting surfaces, but the boss it rides on is not square
with the table. I wouldn't have been surprised at less than 0.001"
over a little more than an inch and a half, but 0.002" was a lot.
I needed to give this some more thought.
I tried a pivot
test on the table support bottom surface against the surface plate
and it pivoted at the center. This showed that the surface was
slightly convex and high in the center. This is no surprise as
sliding surfaces usually pick up more swarf on the outer ends than
they do in the center, and consequently the wear is greater at the
ends of the shorter sliding surface. Because I was still unsure
what to make of the measurements I taken on the boss, I decided
that I would start scraping the table support first. The support
is pretty scarred on the bottom. There are also some wear lines
that are not parallel with the bottom rectangular surface. It
appears to me that the support had been mounted cocked on the
front of the table at some point in the shaper's past. I also
noticed that the way wiper felts on the support base were worn out
and not doing their job of keeping swarf from getting between the
support and the boss. Knowing that wiper felt replacement is often
overlooked, I had purchased enough to last me quite a while. I'd
replace these once I scraped the bottom of the support.
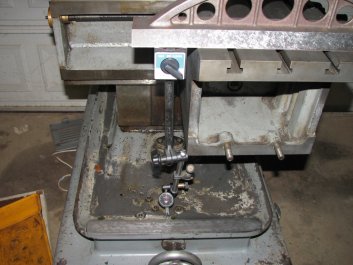
|
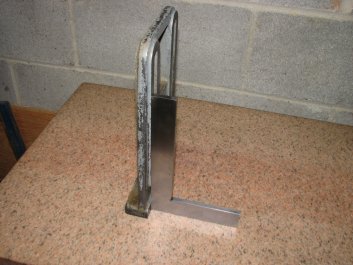
|
Using
the straight edge to support the DTI, the boss appears to
be out of parallel with the table by 0.002" across the 1
9/16" section of the boss.
|
Amazingly,
even though the bearing surface of the table support is
scarred and worn, the attaching surfaces are square with
the bottom.
|
The first print
I took of the table support base showed color in the center, but
more color on one side than the other. This didn't necessarily
mean that one side is more worn as I could have just put a little
more pressure on one side while I was marking it. When a piece is
high in the center, it will rock as you try to print it. Before I
started scraping, I mounted the inked table support to the table.
I would try to wear off the print I had just taken against the
surface of the boss to see if my print matched the front to back
slope of the boss. This should confirm or refute that the table
support base is in the same plane as the boss it rides on.
However, like anyone who has tried to bring a machine into being
square with itself has found out, there is always another issue to
contend with and sometimes they don't make a lot of sense.
The table
support base is L shaped. The lower leg of the L that sticks out
has rounded corners and the side that is flush with the upright
leg has square corners. If I mounted the support with the
leg with rounded corners facing the operator, the base over-hung
the operator side of the boss by about a 5/16". If I turned the
support the opposite direction, it over-hung the inboard side by
1/4". With the rounded corners facing the ram, I could possibly
place a shim between the table and support in order to center the
base on the boss, but I am at a loss as to why this should be
necessary. Judging by aesthetics alone, I assumed that the side
with the rounded corners was meant to face out toward the operator
so the rounded corner wouldn't catch your pant's leg. If my
reasoning is correct, then there's a rather large misalignment of
the table support to the boss. As I said, it doesn't make a lot of
sense.
It has been said
that scraping is easy, but knowing what to scrape takes a lot of
detective work. The same seems to hold true for figuring out what
the machine designer had in mind.
I am trying to
play detective and am coming up with no good explanation for what
I am observing. On the somewhat plus side, the fact that the
support base overhangs the boss and leaves one side of the boss
with no contact could account for more wear on the rear of the
boss than the front, if the L shaped portion was usually mounted
facing the ram. I admit that it's only a guess, but it makes a
little more sense than anything else I can come up with.
I needed to
scrape the support base no matter what the cause of the
misalignment, so I thought I'd start with this surface and think
about the alignment of the support base to the boss a bit more.
Being only a
novice scraper, I have been doing some more reading and watching
some videos about scraping with the Biax in order to improve my
technique. After reading about how your should keep the distance
between each scrape mark about the same as the width of the scrape
mark, I realized I hadn't been doing this as much as I could. I
decided to try to slow down the speed and increase the length of
the stroke to see if I could rough scrape a little more accurately
than I had in the past. I used #2 speed on my Biax 7ELM with about
a 1/2" stroke. With the scraper angled at 45° to the long side of
the support, I moved the Biax over the length of the surface. I
ended up with scrape marks separated by spaces that were about the
same width of the scrapes. This was an improvement over my my
previous technique. It took a couple passes to scrape the color
from the first print. With each new print, I again reversed
direction and ended up with a bunch of X marks on the surface.
Slowly, I gained more bearing points. However, I found that with
the stroke speed slowed down, I needed to hold the Biax handle
tighter against my body to counteract the push of each slower
stroke. If I didn't support the Biax tightly enough, it jumped
around quite a bit.
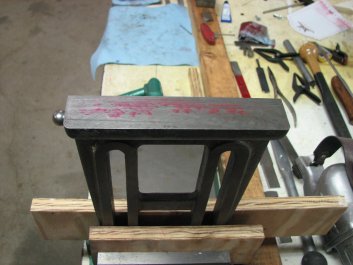
|
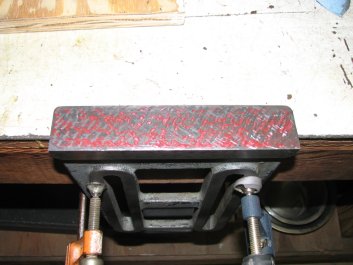
|
To have
an additional way to check the table support boss being
square with the table, I decided to scrape this surface
first.
|
A few
cycles with the Biax and some cuts with a hand scraper to
break up bigger points, I began to get some color across
the bottom surface.
|
After a few
more cycles of scraping with the Biax, I switched to a hand
scraper to start working on the finish passes. I know that it is
possible to finish scrape with the Biax, but I do a better job
with a hand scraper. Once I was pretty close to the bearing I
wanted, about 25 points per inch, it was time to relieve the
center 40% by a small amount. Even though there are way wipers on
the table support, in my short time of using the shaper I found
that a fair amount of swarf lands on the boss that the support
slides against. The swarf will get under the wipers and wear the
outer ends of the support first. Hopefully by relieving the center
portion of the support base, the table support will stay flat for
a longer period of time. Relieving the center section involves
some guess work since you cannot reliably print the area you are
relieving without a specially made template. To relieve the center
40%, I cut in a cross-hatch pattern, 45° one direction, then
switched directions for the next set of passes, with each scrape
going the full width of the surface. I scraped four cycles in each
direction without printing, while offsetting my scrapes by about a
quarter inch each cycle. I tried to use the same pressure for each
scrape. If I have done this correctly, when the ends of the table
support finally wear down so that the center 40% starts bearing on
the boss, I would like the center surface to have a nice array of
bearing points. I don't know if I will achieve this, but that is
my goal.
In the picture
below right, I have the first few passes of relieving done. As you
can see by the stray bearing points in the center section, I still
have to go a bit deeper. I am now beginning to finish scrape the
center section by using shorter strokes and just cutting down the
high points as marked by my camelback placed perpendicular to the
base. Printing this way is not that accurate, but it's better than
scraping blind. I am using a good deal of pressure on each stroke
to increase the depth of the relieved area. Once I get the
relieved area finished, I also need to start splitting some of the
points on the outer ends to get a little more even bearing.
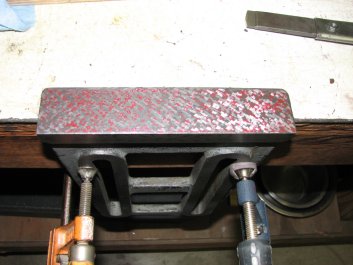
|

|
A few
cycles with a hand scraper and I am starting to get some
pretty good bearing. The next step will be to relieve the
center 40% of the surface.
|
The
base is 7.0" wide, so I relieved the center 2.8" (40%). I
still need to scrape a bit deeper as evidenced by the
stray spots in the center.
|
Toward the end
of the evening, I decided to recheck the measurements I had taken
on the boss in the Y (front to rear) axis with a level. I had seen
a little too much discrepancy in the DTI measurements I had taken
when I had tried to move the straight edge fore and aft on the
table. I rechecked the table for being level and found that it was
off by a half thousandth over the 10" wide table. While the shaper
not being level, wouldn't affect my DTI measurements of the boss,
getting the shaper level to gravity would allow me to use my box
level to confirm the measurements I had taken with the DTI.
Because the shaper didn't stay leveled over a couple week's time
probably meant that the thick rubber padded I had added to the
leveling adjusters were too flexible. While in the process of
readjusting the table level, I noticed that I could move the
level's bubble by stepping on the flange that the adjusters bolt
to. I guess this confirms that the rubber pads were allowing the
machine to move around a lot more than I wanted. I needed to fix
this before I went any further.
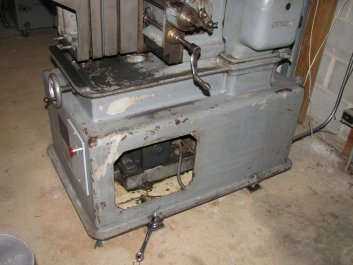
|
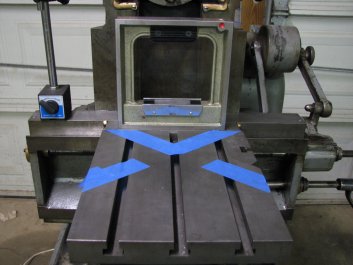
|
The
rubber pads have been removed from the shop made height
adjusters. I'm now thinking that I should have wider
adjuster feet and secure them to the cement floor.
|
It is
easier for me to level a machine by leveling diagonally.
Having the level aligned with the adjusters makes it
easier still. The tape marks allow me to repeat my level
placement.
|
I raised the shaper and
removed the adjusters. I removed the rubber pads and reinstalled
the adjusters. Although the 2" X 3" 3/8" thick steel pads on the
adjusters are about the same size as the commercial adjusters I
purchased for a much heavier machine, I am wondering if a larger
pad would be better on the shaper. The force of the moving ram is
unlike any other machine tool I own. A wider steel pad attached to
the cement floor would probably be an improvement. However, the
new adjusters will have to wait. I needed to take some
measurements, so I now I needed to level the shaper again. As I
have said before, I like to level diagonally. The problem I
encountered with the shaper is that the leveling pads are inboard
from the corners of the rectaganal body of the shaper's base and
can't be seen while I am trying to position the level on the
table. I have found that it is easier to have the level line up
with a imaginary diagonal line between the adjusters. To help me
position the level, I measured the layout of the adjusters. 27"
wide and 22" deep. Since the table is 10" wide and 12" long, I did
some quick math. 22/27 = X/10, X = 8.148" or about 8 5/32". So I
needed my diagonal tape strips to intersect the corners of the 10"
wide table and then intersect at 8 5/32" along the Y axis. With
the tape strips now corresponding to the adjuster locations, it
was somewhat easier to level the shaper.
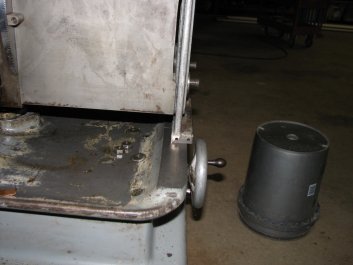
|
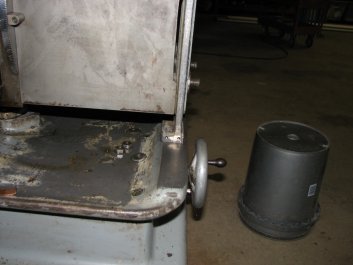
|
Table
support sitting on the boss in the direction that I would
think to be correct except that the front of the support
base overhangs the boss
|
If I
reverse the support, it overhangs the rear of the boss,
but not by as much. While I can correct for this, it
doesn't seem right.
|
With the shaper leveled again, I could now check
the table support boss with the level as well as with an
indicator. This would make it easier to bring the boss into
level with the table. I mounted the table support again to
measure how far out of alignment it was. Facing the direction
that I assumed it was meant to mount, it overhung the front of
the boss by about 5/16". If I reversed the support, it overhung
the rear of the boss by about 1/4". Since I wanted to use the
table support as a final check while scraping the boss, I
decided to machine up a shim to center the support on the boss.
I had no quarter inch flat stock, so I machined the shim from
3/16" and added a couple 1/16" washers until I could purchase
the correct stock. As shown in the picture below left, the shim
and washers centered the support on the boss. I am still at a
loss to explain why the table support doesn't align properly. I
did some looking online and found a few images of Sheldon
shapers with the table support overhanging the front boss.
Apparently mine is not unusual in this respect. I still don't
care for the setup. I think that the more surface the support
base has in contact with the boss, the more evenly it will wear.
I also think my plan of turning the support with the leg to the
inside and using a shim will work fine. It should help keep the
newly scraped surfaces from wearing unevenly.
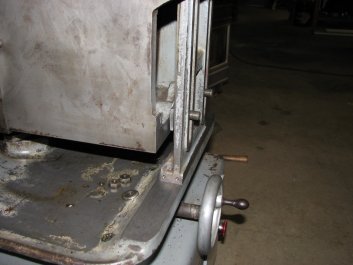
|
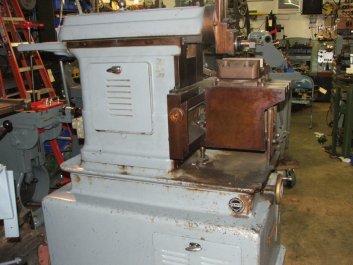
|
I
made a shim from some stock I had on hand and added a
1/16" thick washer behind each leg to get the support
centered on the boss. .
|
I
found a picture online showing another Sheldon shaper
with the table support overhanging the boss. Apparently
this issue wasn't limited to mine.
|
To
scrape the boss, I would need to correct for it being angled
in two directions. The high point, viewed from the front of
the machine, is the front left corner. I used my camelback
straight edge to mark the boss. It showed color only in the
center of the boss. I forgot to take a picture of this, so the
first shot is after a couple passes with the Biax. I am using
a lot more downward pressure as I come to the left front of
the boss. I have a couple thousandths to scrape from the left
front end. I scraped until I had a few spots of color
over the whole boss, then started step scraping to lower the
left side of the boss. I also used a little more pressure on the
front side of the boss to start getting rid of the angle in the
Y axis. In a couple hours, I had brought the surface to within a
thousandth high on the left (X axis) and within a couple tenths
front to back (Y axis). Since I have been scraping with more
pressure on the left side of the boss, the difference between
the peaks and the valleys is as much as 0.0004". This makes it a
little tough to measure the slope of the boss as the indicator
bounces as I crank the table and attached indicator across its
length. I decided to spend a little time refining the surface so
I could get some better accuracy in my measurements. This might
be considered wasted work as I still have a slight angle to the
boss, but I felt that I need to get a more accurate idea of how
much to scrape to get the boss parallel with the table's travel.
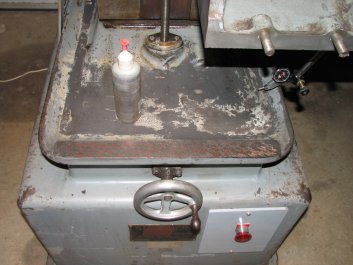
|
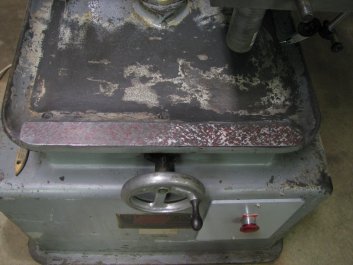
|
Since
I forgot to take a picture before I started scraping,
here's a shot after a few cycles with the Biax and a
couple cycles with a hand scraper.
|
The
boss is still about 0.001" high on the left. I will now
scrape enough cycles to get the surface smooth enough to
map out the slope accurately.
|
After another few cycles of hand scraping, I
had lessened the height between the points and the valleys and
had increased the point count a bit more. I again measured the
slope of the boss in both directions. I was now measuring a
slope of 0.001" over the full 16.5" of the boss with it high
on the left side. Over the 1 9/16" width, I was pretty close
to level. It was time to do one more step scrape of the boss.
I decided to set up the camera and take pictures of the
process of applying color to act as a guide. I rolled marking
fluid on the left side covering about 1/5 of the surface, then
scraped it off with the Biax. Then marked 2/5 and scraped
that. I repeated this until I had marked and scraped the whole
surface. When scraping for bearing points, I would try to
leave spaces between the scrape marks, but the object of step
scraping is to evenly lower one end of the surface, so I kept
the scrape marks close to each other. I also normally reverse
directions on each cycle, but I am more consistent scraping
from right to left and with moderate pressure can scrape
0.0002" per pass. Since I needed to lower the left side by one
thousandth, five passes should get the boss close to level. I
put together an animated gif showing the process. I did forget
to take a picture of the fourth scraping pass, but otherwise,
it shows the process pretty well. I also added two shots of
measuring the surface. The indicator shows about a
ten-thousandth of slope in 16", but it really isn't quite that
close. I went from a very good points count to a very sparse
points count and there are sections of the boss where there
are two or more tenths height difference within a quarter
inch. I will do a bit of hand scraping to get an idea of where
my high and low areas are, then rough and finish scrape from
there. At least I now have a boss that is in the same plane as
the movement of the table.
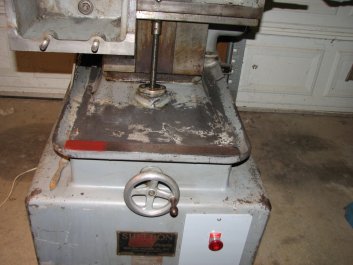
|
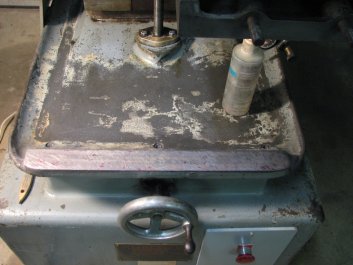
|
Step
scraping the table support boss to remove one
thousandth inch of slope over 16.5". Click image for
animated gif (2.5 megabyte file size).
|
After
the step scraping passes, I went from a decent points
count to next to no points at all, but the boss is now
pretty much level with the table.
|
As usual, making a print of the newly step
scraped surface is a bit of a let down. It now didn't have
much in the way of bearing points. I made a couple passes
just picking the tops off of the few points I did have until
I could get an idea of the high and low areas. I then made a
couple passes at 45° with each scrape covering the entire
width of the boss. I refined the surface a bit more and
decided that it was time to put the level on the boss. I
knew I was close to level, but was pleased to see that the
level's bubble was aligned with the center
indications. Less than a ten-thousandth out over ten inches.
Not too bad at all.
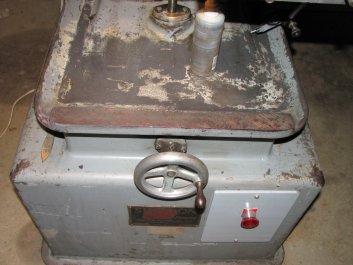
|
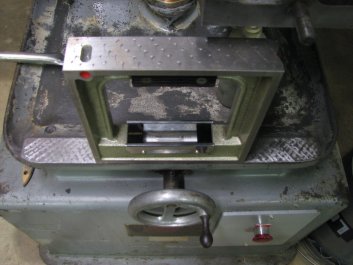
|
After
one pass with the hand scraper, I am beginning to
see where my high and low areas are located. I have
some more scraping to do.
|
Double
checking the plane of the support boss against the
plane of the table on a leveled shaper. I couldn't
have asked for a better reading.
|
Checking the boss over the short side was
a bit trickier. With less than two inches to rest the
level on, the measurement wasn't going to be as accurate
as measuring on the longer axis, but I was just looking
for confirmation that the measurement I had taken with the
DTI was close to what the level showed me. Again, the
bubble lined up with the center marks on the vial. Now all
I needed to do was to print the boss again and start
refining the surface.
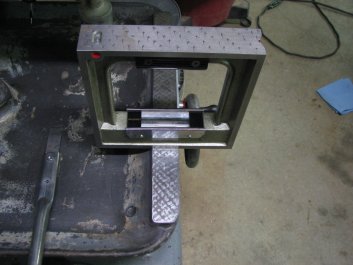
|
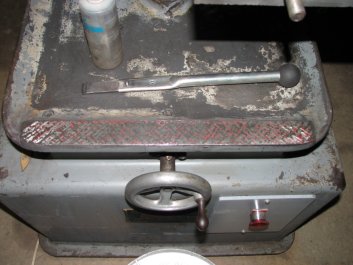
|
With
the level set across the 1 9/16" boss, some
inaccuracy is expected, but the level shows that
this plane is pretty close to level with the
table.
|
Another
couple of cycles with the hand scraper and I am
beginning to see some color across the whole
surface. Finish scraping is the next step.
|
Refining the surface from the
cross-hatch rough scraping I had done went pretty
quickly. I started by scraping off as many high points
as I could get with half inch strokes using the hand
scraper. I kept scraping at a 45°angle and reversed
directions of the angle on each cycle. I continued this
for a few cycles, then switched to scraping off
individual spots. If I had a group of spots angled to
the left, I scraped through them to the right and vise
versa. It took about five more cycles to get to the
picture on the lower left. The boss now had areas of 35
or more points per square inch in some areas and as few
as 25 per inch in others. While I would like to see the
points count to be a little more consistent, my number
of points per square inch is in excess to what's
necessary for this surface. Even though I have been
scraping for almost a decade, I still have much to learn
about getting a consistent pattern and points count on
what I scrape. However, I have gotten a lot quicker at
refining surfaces since I started work on this shaper.
To be able to take a surface from less than one point
per square inch to 25+ in an hour or so is pretty quick
for me.
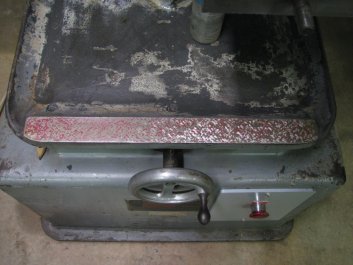
|
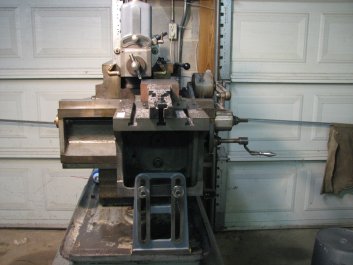
|
I am pretty close to done scraping the
boss. I have a few sparse areas and will scrape
another pass or two, but am pleased with my
progress.
|
Taking a test cut. With one side of the
CI block surface ground, I planed the other
side. The planed surface came out pretty close
to parallel.
|
With all of the scraping done, I
finished up painting the tool head, table support, and
the vise parts. My paint mixture is a little darker
than the paint on the rest of the shaper and looks a
little more blue when not in direct light. In the
picture above right. the tool head is the same color
as the table support, but they look very different in
the picture. Enough about the paint. Time to take a
test cut.
Since the vise still needed to have the rails cut, I
needed to find an alternate means of mounting the 4" X
6" block of cast iron. I would have preferred to mount
it directly to the table, but didn't want to use hold
downs that would need to be removed as I planed the
whole upper surface. I ended up using a two piece
milling vise. It was too tall, so I needed to put
parallels below the cast iron block I was cutting. Not
really the best way to check the accuracy of the cut,
but it would let me test whether the tool head ways
worked better and whether the lock was now working as
designed. I set the ram travel for 7" and set the ram
position to have 1/2" over-run on either side of the
6" block.
I started my cut with the table moving left to right
and got used to the rhythm of the clapper box lifting
at the end of each cut and snapping closed just before
each cut began. About half way through the 4" feed in
the X plane, the sound of the clapper got a bit louder
and the timing of the noise changed. At first I didn't
understand the change in sound and rhythm, but soon
discovered that the ram stroke was lengthening and was
now up to 8". The force of the clapper closing on the
longer stroke made it sound a bit louder. By the end
of the cut, the ram stroke had increased to 10". What
the heck? Something wasn't right. However on the plus
side, I had zeroed the tool head dial and locked the
tool head before I began the cut and when the cut was
done, the tool head had not moved. I wound the table
back to the starting position and set the tool head
for another cut. 0.002" this time instead of 0.005" as
for the first cut. I reset the ram travel to 7" and
began the cut. This time, the ram stroke started
increasing at about 1/4 the way through the 4" cut.
Rather than stop the machine and reset the ram, I just
let it cut so I could check the test block for the top
surface being parallel with the bottom surface. The
stroke had increased to 11" by the end of the cut.
With the top surface of the block planed, I removed
it, put it on the surface plate, and measured it. Even
with the less than accurate two piece vise, the plane
of the top surface was within a half thousandth of the
ground bottom surface across the worst diagonal
measurement. The other diagonal was within a couple
ten-thousandths. It appears that scraping the tool
head, swivel block and gib has helped. The tool head
lock also seems to be working as designed now. I only
have to lightly snug the lock screw to keep the tool
head from creeping down and making the tool bit cut
deeper into the work. So I seem to have succeeded in
fixing the problem that I set out to repair, but have
discovered another issue that needs some attention.
Such is the way it seems to go with old iron. On one
hand, I'm happy that I have been able to take care of
something that needed attention, but I am now playing
detective again to see if I can deduce why the ram
stroke is increasing.
Next installment: trying to figure out the increasing
ram stroke.