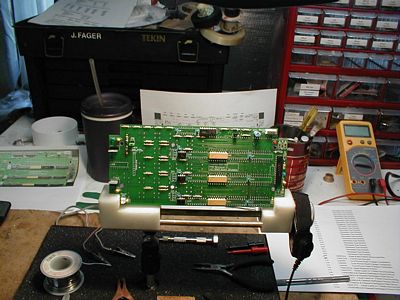
The circuit board is
partially assembled.
|
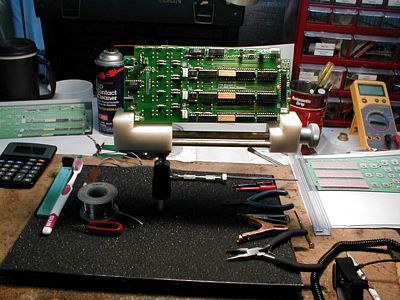
|
The
remainder of the ICs get installed.
|
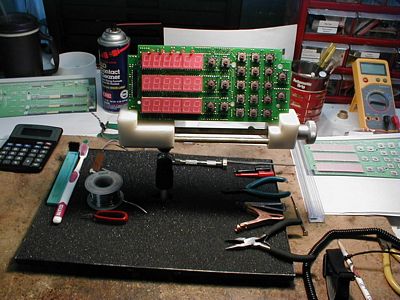
|
The
tactile switches and displays are installed.
|
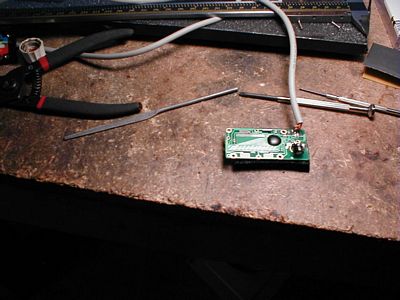
|
Soldering
a cable to a Harbor Freight digital caliper.
|

|
A
close-up of the same. A 100µF electrolytic capacitor is
substituted for the standard button type battery.
|
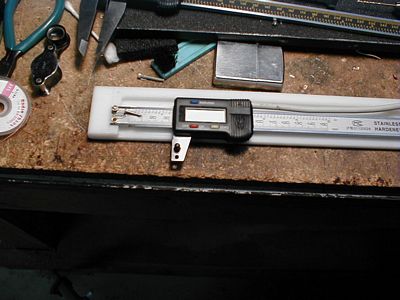
|
With
3-1/2 of the 4 caliper jaws removed, the caliper is transformed into a
digital scale and mounted.
|
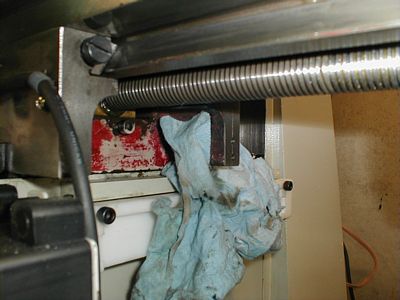
|
Holes
are drilled free-hand in the saddle. It appears that before it
was beige, the saddle was painted red! Well, at least the other
side is beige.
|
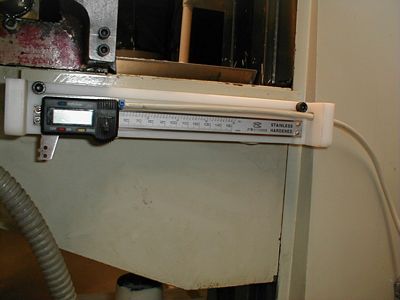
|
The Y
axis scale is partially mounted.
|
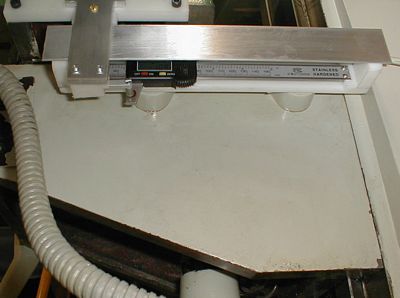
|
Control
arm and cover are installed.
|
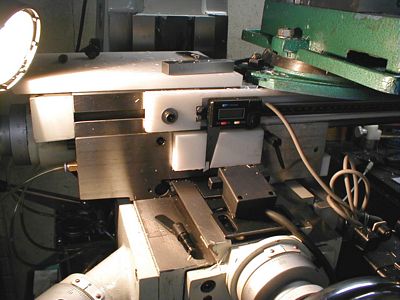
|
Working
on the X axis. This is a temporary scale that will be used until
my new Jenix scale arrives.
|
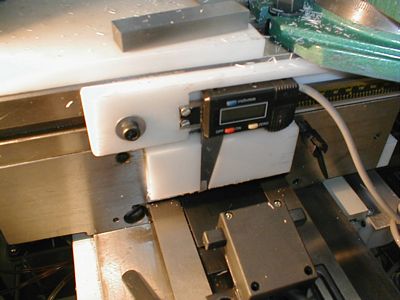
|
The
caliper jaw is embedded into the plastic. Having this much
surface holding the jaw made for good support.
|
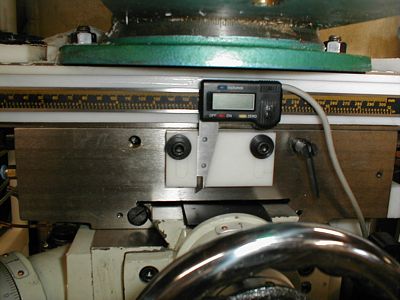
|
Bolt
holes are added.
|
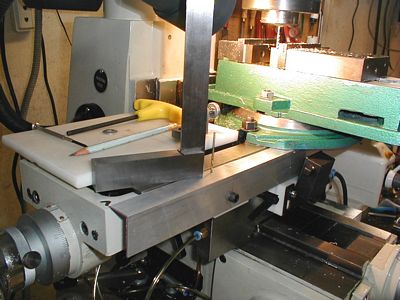
|
Aligning
the holes for the cover. An extra drill bit holds the cover in
place while I measure for the next hole.
|
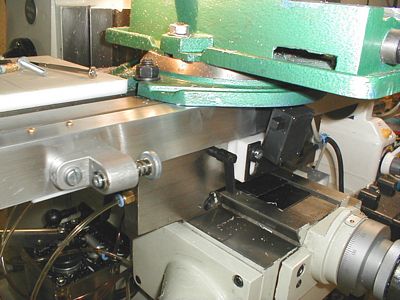
|
The
limit switch is remounted and the bumper is put in place. With
the temporary scale, my X axis was limited to just under 13 inches
until the new scale arrives.
|
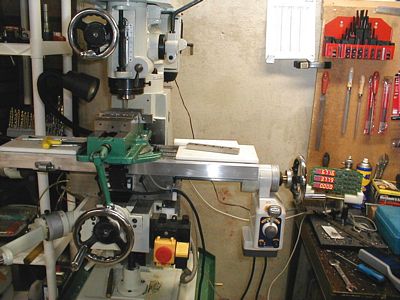
|
Testing
the read-out while still working on the bumper for the right side of
the X axis.
|
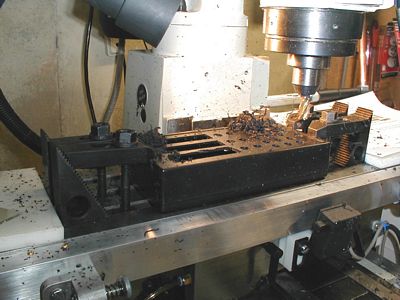
|
Using
the DRO for its first task. Cutting its own housing!
|
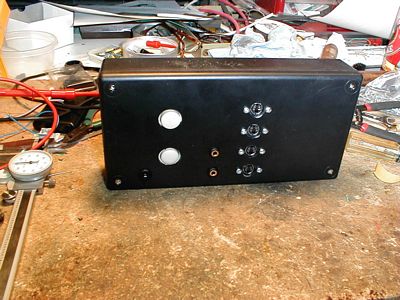
|
Wiring
the housing. The white circles are switches to switch between two
scales on the Z axis and to choose either RPM or electronic edge finder.
|
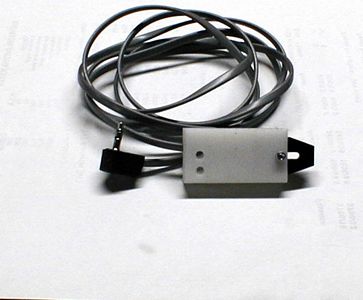
|
This
is the Fairchild photo transistor for measuring spindle speed, housed
inside a liquid and swarf proof HDPE box.
|
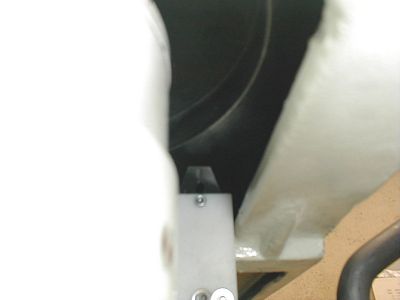
|
And
mounted. Looking up at the under-side of the spindle pulley
(which is a lot more shiny than it looks here).
|
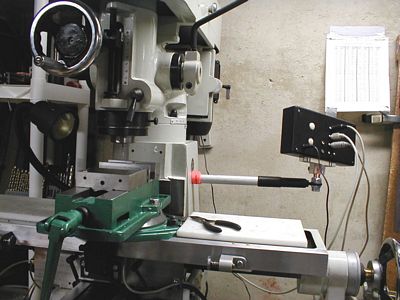
|
An arm
holds the DRO in place and adjusts in length as well as allowing the
unit to swivel.
|
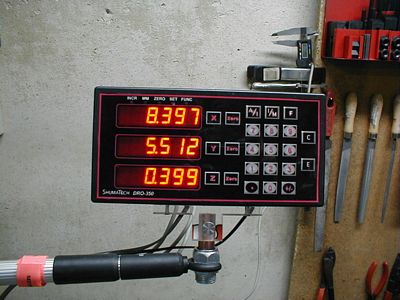
|
Scott
was out of over-lays (and I wasn't crazy about the blue lettering
anyway), so I made my own.
|
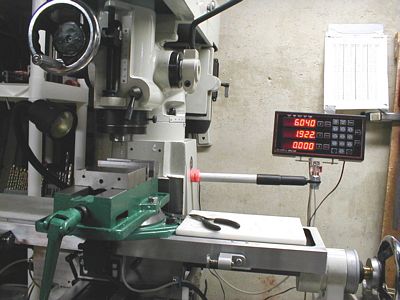
|
Done
for now. Step back and admire one very cool DRO.
My thanks to Scott for a useful and fun project!
|