Tear it down
5-24-00
Well, it's been a little over seven months
since Water Cooler 4 was installed on my Windows box. Since it's
time for a processor upgrade and, of course, I plan to water cool and add
some peltiers to it, I though it would be a good idea to strip it down
and see what 7 months of chillin' does to a rig. During this time
the processor was run mostly at 633 MHz. Yes, it would do more.
No, it wasn't completely stable at anything above 633. If I had one
crash that I could attribute to something other than just the normal Windows
array of crashes, it would be one crash too many. As well as being
my play toy, this box keeps track of my life and I don't take kindly to
down-time.
During the seven months, I ran Rain 1.0.
Always. Now there are those that say that running a software cooler
and peltiers is a bad mix. I am not one of those people. I
tend to think that good insulation is all that is needed to get around
the condensation issues. However, the use of a software cooler does
make for some pretty good temperature swings. Consider that the normal
internal processor idle temp for this setup was about -7°F (seven below
zero) and gaming, CAD work, and a few other uses could push the temperature
into the +60°F range. That's a fairly good swing, but not really
any more than a stock heat sink would produce under some situations. (+75
to +142 for example.)
Aside from just liking the cooler programs
for their power saving aspects, another reason to run Rain was to see how well the
packaging of my cooler held up to the humidity and the perils
of condensation. I have to say that I was impressed. Not
only did the Monokote covering do its job in keeping condensation from
forming inside the peltier assisted, water cooled package, but the use
of dielectric grease completely prevented any corrosion from forming on
the PPGA processor's pins and the slotket's edge connector.
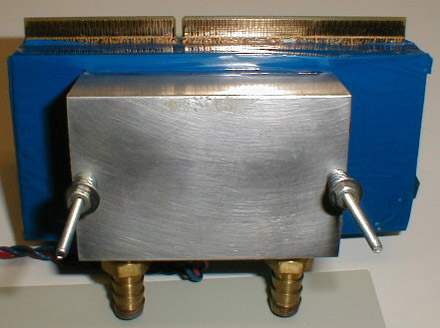 |
I can honestly say that
it was very tough to have to tear this
project apart, but before I moved on to
WC7 and even colder
temps, I needed to know more about the
long term effects of running sub-zero temperatures.
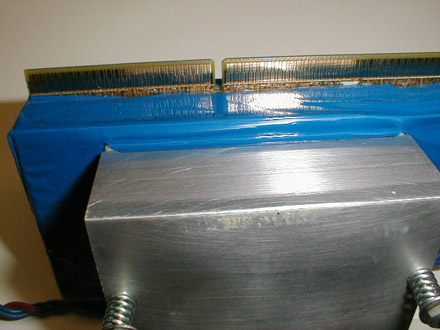 |
The edge connector is
clean. The dielectric grease served
its purpose well. The residue on
the face of the water cooler
block is the adhesive from the duct tape
that held the water block's thermo-sensor in place.
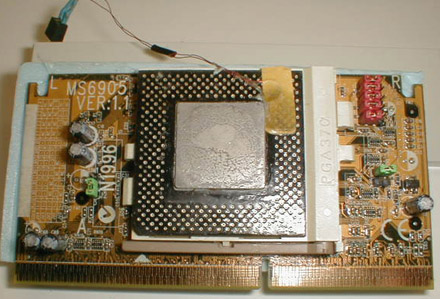 |
No signs of condensation
or corrosion here either. It does have a fairly nice pattern of thermal
grease though! You can see that
both the processor and adapter were coated
with polyurethane, just in case some moisture got in. The yellow
tape holds
another thermo-sensor against the edge
of the slug.
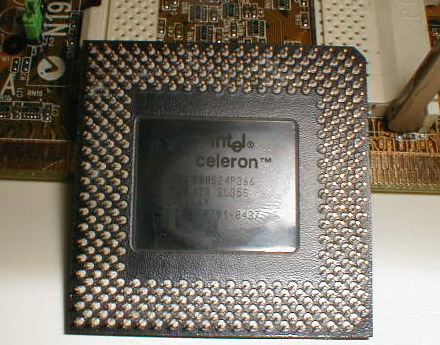 |
Hmmm, aside from my
strategically placed thumb print, this shot shows nothing that shouldn't
be there. No signs of corrosion.
It would appear that the dielectric grease
did its job here also.
All in all, I'm pretty happy with the way
this cooler worked out. I'd say that in this particular situation,
those who predicted that this processor would die a premature death due
to condensation were wrong. It does appear that with a little care,
running cold temps doesn't have to mean that condensation will kill your
processor. Now that the tear down has been completed, I have more
confidence that the next cooler can go a bit colder. Hopefully in
six months or so with the next tear down, I'll be able to report the same
success with WC7.